Introduction
Straw crushers are an important piece of farming equipment for processing crop residues into smaller pieces. Maximizing the efficiency of a straw crusher can help farmers make the most of their straw resources. This blog post will provide tips on how to optimize straw crusher performance to increase output. We’ll discuss straw crusher components, maintenance practices, operational techniques, and more. The goal is to help farmers get the best results from their straw crusher.
Straw Crusher Components
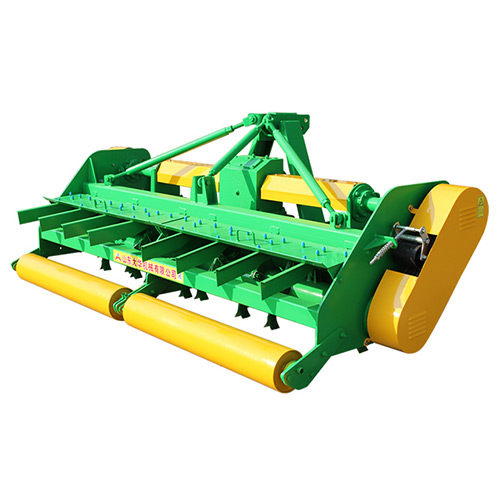
The key components that influence a straw crusher’s efficiency include the feed inlet, rotor, grate bars, and discharge outlet. Paying attention to how these parts function and interact is crucial.
The feed inlet is where straw first enters the machine. It’s important to avoid clogs by only feeding an amount of straw that the crusher can handle smoothly. An inlet that’s too full will cause jams.
Inside the crusher chamber, the rotor plays the main role in breaking up straw. Ensuring rotor blades remain sharp is critical for efficient crushing. Dull blades will struggle to shred straw adequately. Rotor speed also affects output – too slow and straw won’t break down fully, too fast risks wrapping and blocking.
Grate bars sit underneath the rotor and help control the size of crushed straw pieces. Adjusting bar spacing alters the level of fineness. Wider gaps produce larger chunks while narrower gaps create finer material. Clean grate bars unblocked by debris allow for unrestricted flow.
Lastly, the discharge opening needs to efficiently expel crushed straw without clogging. Make sure this exit point remains clear so processed material flows out smoothly.
Routine Maintenance Practices
Conducting regular maintenance is key to maximizing a straw crusher’s performance over the long run. Key tasks include:
- Inspecting and sharpening rotor blades as needed to maintain efficient crushing ability.
- Cleaning out the crusher chamber and clearing any built-up residue to avoid future blockages.
- Checking grate bars for wear and tear, and replacing as necessary to keep the desired sizing.
- Greasing all pivot points and moving parts according to the owner’s manual to ensure smooth operation.
- Checking belts and drive components for wear and tightness, and adjusting/replacing to avoid slippage.
- Performing any repairs promptly to address issues before they worsen and affect output.
Proper maintenance helps extend a straw crusher’s usable lifetime while keeping it running at peak efficiency. Neglecting maintenance tasks can compromise performance over time.
Operational Techniques
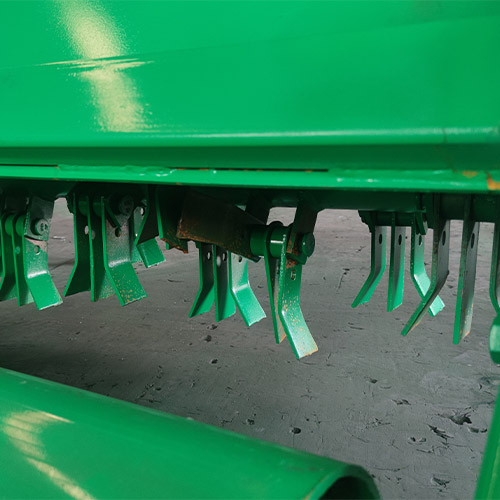
Along with routine maintenance, employing best operational techniques when using a straw crusher can boost its productivity. Some tips include:
- Feeding an even, consistent amount of straw into the inlet to avoid overloading or underfeeding the crusher.
- Adjusting rotor speed based on straw type – drier straw may require a faster speed while wet straw works best at a slower rate.
- Setting the grate bar spacing to achieve the desired size of crushed pieces for intended use such as bedding or composting.
- Stopping periodically to clear any blockages that occur to resume smooth crushing.
- Avoiding foreign objects like rocks that could damage the crusher. Sift straw beforehand if needed.
- Monitoring output to ensure the crusher is functioning as expected and making necessary adjustments.
Proper feeding techniques and adjusting settings based on conditions helps extract the full potential from a straw crusher. With practice, operators can fine-tune their methods.
Table: Recommended Rotor Speeds by Straw Type
Straw Type | Recommended Rotor Speed (rpm) |
---|---|
Wheat | 300-350 |
Rice | 250-300 |
Corn | 350-400 |
Soybean | 300-350 |
Conclusion
With the proper maintenance, operational techniques, and adjustments discussed above, farmers stand to maximize the efficiency and output of their straw crushers. Keeping components in good working order and fine-tuning settings for conditions are key. Following these best practices helps extract the full value from straw resources while extending equipment lifespan. With regular monitoring and care, straw crushers can reliably process high volumes of crop residues over the long term.
FAQs
Here are answers to some frequently asked questions about optimizing straw crusher efficiency:
Q: How often should rotor blades be sharpened?
A: For average use, rotor blades may only need sharpening every 1-2 years. But it depends on straw volume and conditions. Inspect blades regularly and sharpen as soon as cuts appear dull.
Q: What is the ideal moisture level for crushing straw?
A: Straw should be crushed at around 15-20% moisture content. Drier straw may require faster rotor speeds while wet straw above 25% risks wrapping and jamming.
Q: Can a straw crusher be overloaded?
A: Yes, overfeeding a crusher will decrease efficiency and lifespan. Only feed an amount the crusher can handle smoothly based on its design specifications. Stop periodically to clear any blockages.
Q: How do I know if my crusher needs repairs?
A: Signs it needs repair include: reduced throughput, uneven crushing, excessive noise/vibration, or physical damage. Address issues promptly before they worsen by consulting the owner’s manual or an equipment dealer.